Palletizing is a critical process in industries worldwide, where products are stacked and secured onto pallets for shipping or storage. While automation is becoming more common, manual palletizing—where workers perform these tasks by hand—remains common, particularly in warehousing and manufacturing sectors.
However, this widespread practice comes with health and safety risks that cannot be ignored. In this article, we will explore the risks associated with manual palletizing and discuss strategies to mitigate them, ensuring a safer workplace.
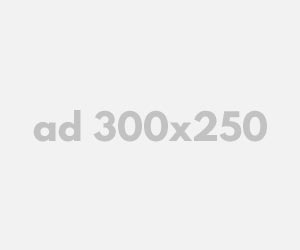
The Risks of Manual Palletizing
Manual palletizing involves workers physically handling products, which exposes them to various risks of injuries. The repetitive nature of this work, combined with the potential for heavy lifting and awkward postures, makes it a primary contributor to workplace ergonomic injuries.
Common Risk Factors
Awkward Postures: Bending, twisting, and other unnatural positions can lead to strains and sprains.
Repetitive Motions: Frequent reaching, lifting, and carrying increase the risk of musculoskeletal disorders (MSDs).
Forceful Exertions: Lifting or carrying heavy loads can cause overexertion injuries.
Pressure Points: Handling cartons or leaning against hard surfaces can result in discomfort or injury.
Static Postures: Holding fixed positions for extended periods can lead to fatigue and musculoskeletal issues.
Palletizing operations can lead to stress, fatigue, anxiety, and other reactions, increasing the risk of musculoskeletal disorders (MSDs).
Personal risk factors such as prior medical history, physical capacity, lifestyle, and habits like smoking and lack of exercise can also contribute to injuries.
These MSDs result in reduced quality of life, chronic disability, psychological distress for workers, increased absenteeism, turnover, and insurance premiums for employers.
Injuries Statistics
In the United States, manual materials handling, including palletizing, is a significant concern. According to the U.S. Bureau of Labor Statistics (BLS) and OSHA, industries that rely heavily on manual handling report higher rates of worker injuries.
In 2023, musculoskeletal disorders accounted for a substantial portion of workplace injuries, with 266,530 cases involving days away from work in 2022 alone.
Risk reduction strategies
Mitigating the risks associated with manual palletizing requires a comprehensive approach that goes beyond standard weight limits for lifting.
Evaluate and Analyze Lifting Processes
Utilize tools like the NIOSH Lift Limit equation and the Composite Lifting Index (CLI) to assess the cumulative physical demands placed on workers. These tools help industrial and safety engineers develop effective prevention plans.
Hierarchy of Controls for MSDs
Eliminate Hazards at the Source: The most effective way to reduce risks is by removing the hazard entirely.
Automate Palletizing: Implementing automated systems removes workers from the most physically demanding tasks, significantly reducing the risk of strains, sprains, and MSDs.
Engage Engineering Teams
By involving engineering teams in the risk assessment and mitigation process, you can ensure that the most appropriate and effective safety measures are implemented. This proactive approach not only enhances worker safety but also contributes to a healthier and more productive working environment.
The palletizing solution
Adopting semi-automated and fully automated palletizing solutions can significantly reduce the risks associated with manual palletizing by leveraging technology to handle repetitive and strenuous tasks.
Semi-Automatic Palletizing
Semi-automated palletizing systems require some level of human interaction, such as supervising or managing the equipment, while machinery performs the bulk of the physical work.
This approach offers greater efficiency compared to manual methods, allowing workers to focus on more complex tasks and reducing the incidence of repetitive strain injuries. Semi-automated systems often incorporate robotic arms or automated conveyors that assist in the stacking and palletizing process without fully eliminating the need for human operators.
Fully Automatic Palletizing
Fully automated palletizing solutions minimize human involvement by utilizing advanced robotics to autonomously handle the entire palletizing process. These robotic palletizers include a large spectrum of solutions.
Automation is no longer reserved for large industrial manufacturers. Automated palletizing is now possible with affordable collaborative robots. Agile, easy to use and program, using a very small footprint, collaborative robot palletizers are widely seen in small to medium-size manufacturers.
Replacing manual labor with robotic palletizers not only enhances workplace safety but also improves operational efficiency, reducing the potential for human error and the risk of workplace injuries.
Automating palletizing enables valuable employees to do more and grow within the company. Robotic palletizer reduces dependency on hard-to-find labor and eliminates jobs that no one wants to do.
Conclusion
Manual palletizing, while essential in many industries, is labor intensive and poses significant health and safety risks to workers. By understanding the risk of injuries and implementing comprehensive strategies to mitigate them, businesses can protect their workforce and improve operational efficiency.
Engage with your engineering teams and explore the potential of automated solutions to ensure a safer future for all employees. Prioritize safety today and reap the benefits of a healthier workplace tomorrow.
GIPHY App Key not set. Please check settings