The speed that top foundries are moving at in their never-ending quest to improve the speed, performance, and efficiency of smartphone chips is truly remarkable. Just this year, TSMC, the world’s leading foundry, is set to start mass production of 2nm chips. Next year, the Taiwan-based company says that it will start mass production of 1.6nm chips. As these process node numbers decline, the size of the transistors inside these chips shrink which allows more transistors to be shoehorned inside them.
This is important because smaller transistors mean that more can fit into a given area of the chip. This metric, known as transistor density, usually rises when the process node goes down. The transistor count of a chip also is important because typically the larger number of transistors in a chip, the more powerful and energy-efficient these semiconductors are. Consider the amazing drop in process nodes that we have seen just over the last few years.
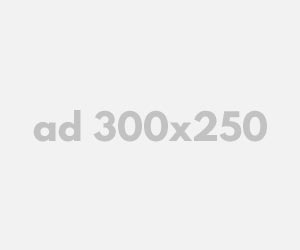
For example, in 2019 the iPhone 11 series was powered by the 7nm A13 Bionic application processor (AP) carrying 8.5 billion transistors. This past September, the iPhone 16 Pro Max was released with the 3nm A18 Pro AP under the hood. While Apple never released the transistor count for the chipset, the component most likely features over 20 billion transistors considering that the A17 Pro has 19 billion transistors.
TSMC is on a roll as it just reported fourth-quarter revenue up 37% year-over-year to $26.88 billion. What TSMC calls “smartphone seasonality” will lead to a sequential decline in its top line for Q1 2025 although on an annual basis, first quarter gross will rise 34.7%.
With its 2nm chip production, TSMC will start using Gate-All-Around (GAA) transistors which use vertically stacked horizontal nanosheets allowing the gate to cover all four sides of the channel preventing current leaks and improving the drive current. The result is higher-performing chips with more energy efficiency. When it starts production of 1.6nm chips, TSMC will debut backside power delivery (BPD). BPD moves power delivery from the front of a silicon wafer where it leaves less space for transistors, to the back where it is unimpeded by other wires.
The A18 Pro application processor, made using TSMC’s second-gen 3nm node, powers the iPhone 16 Pro and Pro Max models. | Image credit-Apple
To show you how far we’ve come, the original iPhone, released in 2007, used a chip built on the 90nm process node. The upcoming iPhone 17 series due to be launched this September will be powered by the 3nm A19 and A19 Pro APs which will be made using TSMC’s third-generation 3nm node (N3P). As a result, Apple should be able introduce the first iPhone to run on 2nm silicon with the 2026 iPhone 18 series.
When will we see the first iPhone to feature an AP made using the 1.6nm node? We will have to get back to you on that. Meanwhile, TSMC says that 1.6nm chips will offer an 8% to 10% improvement in speed at the same power compared tot he 2nm node.
GIPHY App Key not set. Please check settings