Watch Out visualizes a highly automated workcell that can fit into a container. Source: Watch Out
Manufacturers face widespread shortages of skilled labor, but more intelligent automation could alleviate the problem, according to Watch Out. The company has developed highly automated workcells to make production more flexible and less labor-intensive.
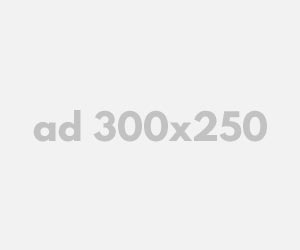
Nearly 2 million U.S. manufacturing jobs could go unfilled through 2033, according to a report from Deloitte and The Manufacturing Institute.
Watch Out offers machining cells that use patented sensors and machine learning for precision manufacturing in aerospace and defense, automotive, medical, and other industries. The Montreal-based company claimed that it offers “Level 5” autonomy for applications such as materials handling, machining, and inspection.
Watch Out starts in aerospace
In 2012, Sébastian Laporte partnered with Frédéric Perret to launch a precision manufacturer for aerospace. He learned to program some of the first CNC machines in France, said Bernard Marietteexecutive chairman at Watch Out.
“Sébastian learned the limits of these machines and recognized the problem of retraining staffers,” Mariette told The Robot Report. “He also built software to analyze the exact dimensions of tiny quartz watch pieces in oil, and Rolex later bought the intellectual property from him.”
In 2016, Laporte and Perret launched Watch Out, and Mariette joined them in 2019. The company designed high-speed connectivity and proprietary sensors into its system to start with the data and deep learning rather than the CNC machining, Mariette said.
“We designed the system from scratch to link the sensors directly to FANUC‘s CNC, which solved the first problem of collecting frugal data,” he said. “The cameras in the machine monitor the position of the parts and the tool itself. Because we have control, we work in nanoseconds and 2 microns instead of 6 for quality control. We’re able to measure every single piece rather than one piece every 1,000 or 5,000, and we’re able to analyze with a microscope.”
Watch Out can also control the amount of aggregated data it collects for continuous learning without losing explainability. “All data related to the customers’ products stays with them,” he said.
Traceability is particularly important in the mass production of medical items such as bone pins, aerospace parts, and luxury goods, Mariette said. In addition, the workcell can include up to three stacks of 25 tools apiece.
The company has about 70 employees in a Precision Machining business unit and an Autonomous Solutions business unit. It has workshops in Bonneville, France, and Dorval, Canada. Watch Out’s investors and customers include LISI Aerospace, a supplier to Airbus and Boeing.
“Startups need vision, resilience, and the support of a big company,” Mariette said. “LISI believed in us and really helped us develop our system.”
Watch Out has created an Autonomous Solutions business unit. Source: Watch Out
AI allows machining to adjust itself
Watch Out said its artificial intelligence eliminates the need for human intervention, from managing CAD files to inspecting parts. Its AI can also handle new work orders, calibration and optimization, and dynamic adjustments to series production.
“Before, if you wanted to change a part to be produced, you’d have to have an industrial person to analyze the plan,” Mariette said. “Then you have to have somebody who knows code for the machine. Then you have somebody who tests the code. Then you have to adjust the code. Then you can go to production. And that would take like from half a day to two days sometimes for a very difficult alloy.”
“In our case, it’s half an hour maximum because you put the CAD file in the machine, and the machine designs its own process, chooses its own tools, and makes a first run,” he explained. “If this first run of five pieces is not right, it adjusts itself, makes another five runs, and so on.”
“That means we will be able to change production paths during weekends, at night, without having the whole process stop,” said Mariette. “The system is designed to run autonomously for at least 48 hours completely autonomously.”
Watch Out envisions flexible and precise cells as microfactories. Source: Watch Out
Adoption enables reshoring of production
Do factory workers see “lights-out” promises as a threat to their jobs?
“We’re not taking jobs away,” replied Mariette. “We’re doing the opposite, by enabling reshoring. Even with full automation, a state-of-the-art factory today will still need some higher-level staffers and logistical people.”
“Today, 40 traditional machines need 40 people; with our system, you’d need 10, but we don’t yet have automatic feeding of parts from stock,” he added.
“In a Watch Out workcell, AI drives the process and makes decisions in real time,” Mariette said. “There may be multiple robot arms and an inspection module — the entire product journey is in the cell, making it a microfactory. In addition, the whole cell can go in a standard container.”
RaaS can help with ROI, says Watch Out
In much of manufacturing, the standard practice is to buy a machine and then amortize it over five years, noted Mariette. With adaptive workcells, there is no obsolescence, because they know when to change parts before they break, he said.
Watch Out offers its systems through a subscription or robotics-as-a-service (RaaS) model.
“It’s not about capex (capital expenditure) anymore,” Mariette said. “It’s about having fewer machines but full utilization.”
The Watch Out workcell has been available for the past year, and the company is looking to expand from France, Switzerland, and Canada to the U.S. and globally. It expected to triple its 2022 revenues, with $30 million CAD ($20 million U.S.) in sales in 2024.
Register today to save 40% on conference passes!
GIPHY App Key not set. Please check settings