In theory, one of the main applications for robotsshould be operating in environments that (for whatever reason) are too dangerous for humans. I say “in theory” because in practice it’s difficult to get robots to do useful stuff in semi-structured or unstructured environments without direct human supervision. This is why there’s been some emphasis recently on teleoperation: Human software teaming up with robot hardware can be a very effective combination.
For this combination to work, you need two things. First, an intuitive control system that lets the user embody themselves in the robot to pilot it effectively. And second, a robot that can deliver on the kind of embodiment that the human pilot needs. The second bit is the more challenging, because humans have very high standards for mobility, strength, and dexterity. But researchers at the Italian Institute of Technology( IIT) have a system that manages to check both boxes, thanks to its enormously powerful quadruped, which now sports a pair of massive arms on its head.
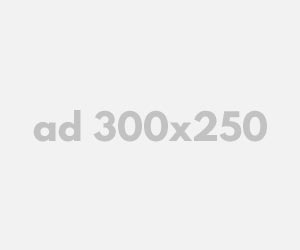
“The primary goal of this project, conducted in collaboration with INAILis to extend human capabilities to the robot, allowing operators to perform complex tasks remotely in hazardous and unstructured environments to mitigate risks to their safety by exploiting the robot’s capabilities,” explains Claudio Seminiwho leads the Robot Teleoperativo project at IIT. The project is based around the HyQReal hydraulic quadruped, the most recent addition to IIT’s quadruped family.
Hydraulics have been very visibly falling out of favor in robotics, because they’re complicated and messy, and in general robots don’t need the absurd power density that comes with hydraulics. But there are still a few robots in active development that use hydraulics specifically because of all that power. If your robot needs to be highly dynamic or lift really heavy things, hydraulics are, at least for now, where it’s at.
IIT’s HyQReal quadruped is one of those robots. If you need something that can carry a big payload, like a pair of massive arms, this is your robot. Back in 2019, we saw HyQReal pulling a three-tonne airplane. HyQReal itself weighs 140 kilograms, and its knee joints can output up to 300 newton-meters of torque. The hydraulic system is powered by onboard batteries and can provide up to 4 kilowatts of power. It also uses some of Moog’s lovely integrated smart actuatorswhich sadly don’t seem to be in development anymore. Beyond just lifting heavy things, HyQReal’s mass and power make it a very stable platform, and its aluminum roll cage and Kevlar skin ensure robustness.
The HyQReal hydraulic quadruped is tethered for power during experiments at IIT, but it can also run on battery power.IIT
The arms that HyQReal is carrying are IIT-INAIL armswhich weigh 10 kg each and have a payload of 5 kg per arm. To put that in perspective, the maximum payload of a Boston Dynamics Spot robot is only 14 kg. The head-mounted configuration of the arms means they can reach the ground, and they also have an overlapping workspace to enable bimanual manipulation, which is enhanced by HyQReal’s ability to move its body to assist the arms with their reach. “The development of core actuation technologies with high power, low weight, and advanced control has been a key enabler in our efforts,” says Nikos tsagarakishead of the HHCM Lab at IIT. “These technologies have allowed us to realize a low-weight bimanual manipulation system with high payload capacity and large workspace, suitable for integration with HyQReal.”
Maximizing reachable space is important, because the robot will be under the remote control of a human, who probably has no particular interest in or care for mechanical or power constraints—they just want to get the job done.
To get the job done, IIT has developed a teleoperation system, which is weird-looking because it features a very large workspace that allows the user to leverage more of the robot’s full range of motion. Having tried a bunch of different robotic telepresence systems, I can vouch for how important this is: It’s super annoying to be doing some task through telepresence, and then hit a joint limit on the robot and have to pause to reset your arm position. “That is why it is important to study operators’ quality of experience. It allows us to design the haptic and teleoperation systems appropriately because it provides insights into the levels of delight or frustration associated with immersive visualization, haptic feedback, robot control, and task performance,” confirms Ioannis Sarakoglouwho is responsible for the development of the haptic teleoperation technologies in the HHCM Lab. The whole thing takes place in a fully immersive VR environment, of course, with some clever bandwidth optimization inspired by the way humans see that transmits higher-resolution images only where the user is looking.
HyQReal’s telepresence control system offers haptic feedback and a large workspace.IIT
The system is designed to be used in hazardous environments where you wouldn’t want to send a human. That’s why IIT’s partner on this project is INAILItaly’s National Institute for Insurance Against Accidents at Work, which is understandably quite interested in finding ways in which robots can be used to keep humans out of harm’s way.
In tests with Italian firefighters in 2022 (using an earlier version of the robot with a single arm), operators were able to use the system to extinguish a simulated tunnel fire. It’s a good first step, but Semini has plans to push the system to handle “more complex, heavy, and demanding tasks, which will better show its potential for real-world applications.”
As always with robots and real-world applications, there’s still a lot of work to be done, Semini says. “The reliability and durability of the systems in extreme environments have to be improved,” he says. “For instance, the robot must endure intense heat and prolonged flame exposure in firefighting without compromising its operational performance or structural integrity.” There’s also managing the robot’s energy consumption (which is not small) to give it a useful operating time, and managing the amount of information presented to the operator to boost situational awareness while still keeping things streamlined and efficient. “Overloading operators with too much information increases cognitive burden, while too little can lead to errors and reduce situational awareness,” says Yonas Tefera, who lead the development of the immersive interface. “Advances in immersive mixed-reality interfaces and multimodal controls, such as voice commands and eye tracking, are expected to improve efficiency and reduce fatigue in the future.”
There’s a lot of crossover here with the goals of the DARPA Robotics Challenge for humanoid robots, except IIT’s system is arguably much more realistically deployable than any of those humanoids are, at least in the near term. While we’re just starting to see the potential of humanoids in carefully controlled environment, quadrupeds are already out there in the world, proving how reliable their four-legged mobility is. Manipulation is the obvious next step, but it has to be more than just opening doors. We need it to use tools, lift debris, and all that other DARPA Robotics Challenge stuff that will keep humans safe. That’s what Robot Teleoperativo is trying to make real.
You can find more detail about the Robot Teleoperativo project in this paperpresented in November at the 2024 IEEE Conference on Telepresence, in Pasadena, Calif.
From Your Site Articles
Related Articles Around the Web
GIPHY App Key not set. Please check settings