Palletizing isn’t one-size-fits-all. From manual stacking to high-speed robotics, businesses have a range of options to streamline operations, reduce labor dependency, and boost efficiency. But which solution is best for you? Whether you’re dealing with space constraints, high product variety, or scalability concerns, understanding the landscape is key. Let’s break down the pros, cons, and best fits for each approach—so you can make the smartest choice for your operation.
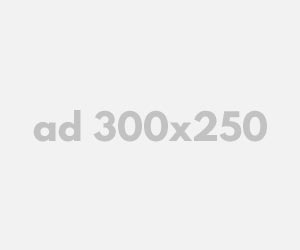
1. Manual palletizing
Manual palletizing involves human labor to stack and organize products onto pallets. It remains a common practice, particularly in smaller operations or facilities with low production volumes.
Advantages:
Low initial investment
Flexibility to handle diverse product types and irregular schedules
Minimal technical requirements
Challenges:
High labor costs, especially with rising wages
Increased risk of workplace injuries due to repetitive motions and heavy lifting
Inconsistent stacking quality and slower throughput
Difficult to scale for higher production demands
Best For: Small businesses or operations with low and inconsistent palletizing needs.
2. Traditional robotic palletizing
Traditional robotic palletizers are industrial robots designed to handle repetitive palletizing tasks. These systems are highly versatile and capable of managing heavy loads with precision.
Advantages:
High speed and accuracy
Reliable and consistent stacking quality
Can handle heavy loads and operate in harsh environments
Reduces labor dependency
Challenges:
High initial costs and longer implementation timelines
Requires significant floor space
Limited flexibility for frequently changing production needs
Best For: Large-scale operations with stable, high-volume palletizing requirements.
3. Collaborative robots (cobots)
Collaborative robots, or cobots, are designed to work safely alongside humans. They offer a flexible and user-friendly approach to automation, making them increasingly popular in various industries.
Advantages:
Easier to implement and program compared to traditional robots
Smaller footprint, ideal for facilities with space constraints
Cost-effective for small to medium-sized operations
Adaptable to changing production requirements
Challenges:
Slower cycle times compared to traditional robots
Limited payload capacity, which may not be suitable for heavy products
Best For: Small to medium-sized businesses looking for flexible, scalable automation.
4. Centralized palletizing systems
Centralized palletizing involves a single, dedicated area where products from multiple production lines are routed for palletizing. This approach allows businesses to consolidate resources and reduce duplication.
Advantages:
Cost-effective for facilities with multiple production lines
Enables efficient use of high-speed robotic systems
Reduces equipment redundancy
Challenges:
High complexity in conveyor routing and product tracking
Increased risk of bottlenecks due to reliance on a single system
Less flexible for line-specific customization
Best For: High-volume facilities with multiple production lines and centralized operations.
5. End-of-Line palletizing systems
End-of-line palletizing involves placing automated palletizers directly at the end of individual production lines. This decentralized approach allows each line to operate independently.
Advantages:
Eliminates bottlenecks by decoupling production lines
Greater flexibility to customize systems for specific product needs
Simplifies product tracking and reduces conveyor requirements
Challenges:
Higher initial investment due to the need for multiple systems
Requires more floor space compared to centralized systems
Best For: Facilities with diverse product lines requiring customized palletizing solutions.
6. Custom-Engineered palletizing solutions
Custom-engineered solutions are tailored to meet specific operational needs. These systems are designed from the ground up to accommodate unique product types, layouts, and production requirements.
Advantages:
Fully optimized for unique processes and workflows
Can handle unconventional product shapes or sizes
Provides maximum efficiency for highly specialized operations
Challenges:
High costs and lengthy implementation timelines
Greater reliance on external vendors for updates and maintenance
Best For: Operations with highly specific or non-standard requirements that off-the-shelf solutions cannot address.
7. Pre-Engineered palletizing solutions
Pre-engineered solutions are standardized systems designed for rapid deployment and ease of use. They offer a balance between customization and affordability.
Advantages:
Shorter lead times and faster implementation
Lower cost compared to custom-engineered systems
Proven reliability and reduced risk
Challenges:
Limited flexibility for unique or evolving needs
May not fully optimize complex workflows
Best For: Businesses seeking cost-effective, reliable automation for common palletizing tasks.
8. Lean Robotics for palletizing
Lean Robotics is a streamlined approach to automation that focuses on simplicity, adaptability, and rapid deployment. This method prioritizes minimal downtime and scalable solutions, making it ideal for dynamic environments.
Advantages:
Quick implementation and ROI
Modular and flexible design
Simplifies automation for non-experts
Challenges:
May require adjustments for highly complex processes
Best For: Small to medium-sized businesses seeking a practical, scalable introduction to automation.
How to choose the right solution
Selecting the right palletizing solution requires a thorough assessment of your operational needs, including:
Production Volume: High-volume operations benefit from centralized or traditional robotic systems, while low to medium volumes are better suited to cobots or Lean Robotics.
Product Diversity: Businesses with diverse product lines should consider flexible systems like cobots or end-of-line palletizing.
Budget: Pre-engineered and Lean Robotics solutions offer cost-effective entry points, while custom-engineered systems cater to unique needs at a higher cost.
Space Constraints: Cobots and Lean Robotics solutions are ideal for facilities with limited floor space.
Scalability: Modular systems, such as Lean Robotics, allow businesses to grow incrementally, avoiding large upfront investments.
Conclusion
With a wide range of palletizing solutions available, finding the right fit comes down to your specific needs—whether it’s flexibility, scalability, or cost efficiency. Understanding the advantages and trade-offs of each option allows you to make a strategic choice that enhances automation, optimizes workflows, and keeps your operations competitive in a rapidly evolving industry. Take a closer look with our Automated Palletizing Buyer’s Guide to see which option best suits your needs or contact one of our experts for advice!
GIPHY App Key not set. Please check settings