An automated gripper changer is part of the CubeBOX machine tending workcell shown here. Source: Tezmaksan Robot Technologies
Production manufacturing demands are increasingly diverse, so adaptability and efficiency are essential, according to Hakan Aydogdu, CEO of Tezmaksan Robot Technologies. Automatic gripper changes provide a practical solution for CNC machines to transition seamlessly between tasks without manual intervention, he said.
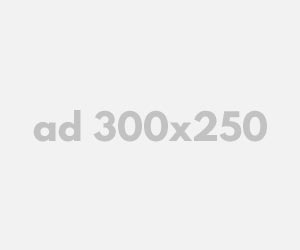
Aydogdu explained how manufacturers can optimize their CNC (computer numerical control) machine operations with automatic gripper changes.
Traditional CNC setups often require manual adjustments when switching between different workpieces. These manual interventions not only consume valuable time but also increase the risk of errors, leading to production bottlenecks.
Similar to a traffic jam, bottlenecks are often a localized issue that cause widespread disruption. In industries that depend on varied production runs or customized orders, such delays can disrupt schedules and escalate costs.
Automatic changes of end effectors address these challenges by allowing CNC machines to quickly adapt to different tasks. By automating transitions, manufacturers can maintain a steady workflow and meet demanding delivery schedules.
Register today to save 40% on conference passes!
Gripper changes ease high-mix, low-volume production
High-mix, low-volume production environments — characterized by frequent customizations and small batch sizes — rely on quick adaptability to remain competitive.
Automatic gripper changes allow CNC machines to handle varying workpieces efficiently without interrupting workflows. This flexibility lets manufacturers meet diverse customer requirements without compromising throughput.
Gripper changes enable CNC machines to handle different workpieces. Source: Tezmaksan Robot Technologies
Consistency in positioning and repeatability are critical for producing high-quality components. In industries like aerospace and automotive, even minor deviations can have significant consequences.
Manual adjustments during production can introduce variability, but automatic gripper changes ensure accurate and repeatable transitions. This leads to higher quality outputs and fewer defects, noted Tezmaksan Robot Technologies.
Automation can help industry advance
The integration of automation technologies such as automatic gripper changes aligns with the broader goals of Industry 5.0 — combining digitalization with human-centric production strategies, said Aydogdu. By adopting these solutions, manufacturers can achieve greater efficiency, precision, and adaptability while empowering their workforce with intuitive tools.
Retrofitting existing CNC machines with automation capabilities is a practical solution for small to midsized enterprises (SMEs) looking to modernize without incurring the high costs of new equipment. Hardware-agnostic systens allow manufacturers to enhance their legacy machines’ functionality, extending their operational lifespan and delaying the need for costly replacements.
Modern automated systems are designed for ease of integration. Their plug-and-play design simplifies adoption, making it feasible for SMEs to incrementally upgrade their production capabilities. This approach bridges the gap between current operations and the demands of a more digitalized manufacturing environment.
For insance, Tezmaksan said its CubeBOX CNC automation systems integrate automatic gripper changes into CNC workflows, enabling machines to easily move between tasks. This innovation is intended to help manufacturers balancing diverse production requirements with the need for high throughput and tight delivery schedules.
By incorporating automatic gripper changes, the CubeBOX system offers a single setup for manufacturers to perform multiple machining tasks. This minimizes manual intervention, reduces errors, and ensures consistent quality across production runs, Aydogdu said.
The CubeBOX system’s modular design and compatibility with various CNC machines make it an accessible and cost-effective option for modernizing operations.
About the author
Hakan Aydogdu is CEO of Istanbul-based Tezmaksan Robot Technologies, which manufactures CNC automation system.
Tezmaksan offers more information about how CubeBOX CNC automation systems can enhance operations at its website and through its specialists.
GIPHY App Key not set. Please check settings