Universal Robots and Raise Robotics said the autonomous system pays for itself within one 13-floor project. | Source: Universal Robots
Up to 1,000 ft. into the air, construction workers need extensive safety rigging to install glass panel brackets. This essential task not only puts employees in danger, but it’s also repetitive and boring. To keep workers safe and allow them to do more high-value work, Harmon Inc., a U.S.-based glazing company, is automating the process with technology from Raise Robotics and Universal Robots A/S.
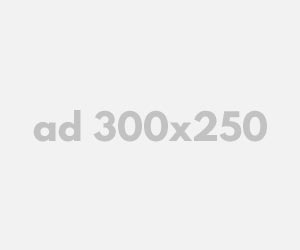
Harmon is an early adopter of this technology, and so far, said it has seen a fast return on investment (ROI). In addition, the Bloomington, Minn.-based building façade company said the robotic system has improved worker safety, as well as consistency and precision in installation. The three partners said the robots provide a 3x multiplier on manual labor and provide a payoff within one 13-floor project.
Traditionally, to install fasteners for glass façade panels on high-rise buildings, workers need to align, drill, and torque brackets in place to precise specifications, all while hanging off the side of a building. Not only is the job not ergonomic, but there is also a significant chance for injury if a tool or bracket falls to the ground below, where other workers may be.
“Safety is always first in mind,” said Don Birmingham, general superintendent at Harmon. “If you can efficiently do a job and take all the safety risks out of it, I think any contractor would sign up for that. As far as the workers, I think they’d much rather be inside the handrail operating a robot than hanging off the edge of the building.”
Raise Robotics uses two UR20 arms
Raise Robotics uses two UR20 collaborative robot arms from Universal Robots for the innovative construction platform. The San Francisco-based company has mounted these two cobots on each mobile robot base. The small footprint and control boxes of the UR20 make them easy to integrate into a mobile application.
“Because Universal Robots has done a great job of making their arms very power-efficient, as well as making it easy to integrate into a DC power solution, we can directly connect our arms to the battery and have our robots operating fully, wirelessly on a construction site,” said Gary Chen, co-founder of Raise Robotics.
In addition, the UR20’s IP65 rating provides confidence for Raise’s customers in using the robots even in inclement environments including dust and rain, as well as extreme temperatures. The company has run the robot successfully from 20°F below zero up to 120°F.
To develop its system, Raise said it used a wide variety of resources from Universal Robots, including online technical documentation and support via myUR. It also used the forums on both the Universal Robots website as well as their GitHub.
“Support from UR has been fantastic,” noted Conley Oster, the co-founder of Raise Robotics. “Any issues that we ran into or any questions that we had early on, we had a dedicated applications engineer from UR that was able to help us. The UR community and forums were extremely helpful to us as well. We were always able to come up with a solution in a timely manner.”
Harmon says robotics reduces manual requirements
Harmon reported a number of improvements since deploying the Raise Robotics system. For example, the manual installation process for façade brackets typically requires two to four workers. In comparison, the robot requires only one person to manage it per installation location.
“It’s a 3x multiplier on traditional labor,” said Oster. That multiplier provides fast ROI for the robot, typically providing breakeven for the robot at about 13 floors based on a monthly lease and amortizing the robot across the number of installations on each floor.
The system didn’t just work faster than manual labor; it was also more accurate, precise, and consistent, the companies said.
“In manual installs, around 30% of all fasteners typically aren’t installed in the right spot,” Oster said. “Using a robot like ours in conjunction with total stations allows us to accurately place fasteners on the building’s edge or within the building’s core. We can install within plus or minus three-sixteenths of an inch, which is far superior to what we’ve seen in manual installations.”
Finally, the system also includes software that provides immediate insight and historical logs of on-site data. This gives exact torque values and alignment for every bracket in real time, as opposed to random quality inspections that are typically done a few times on each floor.
Harmon had “as-built” data, which allowed its team to adjust anchor positioning before the glass walls were installed.
“I think the most benefit we got was the reports of where the anchors were installed,” Harmon’s Birmingham said. “The sooner we found any deviations beyond specs, the easier it was to eliminate them going forward.”
Register today to save 40% on conference passes!
GIPHY App Key not set. Please check settings