Two Glacier systems at work in an MRF in Chicago. The robots can sort up to 45 items per minute. | Source: Areeb Malik, co-founder of Glacier, on LinkedIn
Glacier, which uses artificial intelligence and robotics to efficiently sort recyclable materials, today announced that it has raised $16 million in Series A funding. The company also said Recology’s King County Material Recovery Facility, or MRF, in Seattle has deployed a fleet of its AI recycling robots.
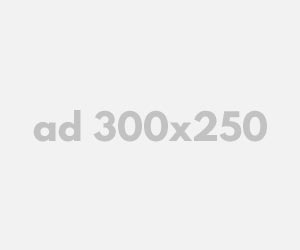
San Francisco-based Glacier said this investment caps a breakthrough period during which it expanded its presence to markets including San Francisco, Los Angeles, Chicago, Detroit, and Phoenix.
“The funding is not only an incredible testament to this growth trajectory that we’re on, on our quest to enable circular manufacturing; but we’re using the funding in a couple of notable ways,” Rebecca Hu-Thrams, co-founder and CEO of Glacier, told The Robot Report. “The first is just to make our hardware, including our robot and our vision systems, increasingly more scalable and faster to deploy.”
Glacier has assembled robots to tackle the unpredictable nature of recycling streams. Its computer vision and AI technology must identify and sort over 30 different types of materials, which can range from common items such as PET plastic and aluminum cans to specific packaging types like toothpaste tubes, cat food tins.
Glacier builds out data flywheel
Hu-Thrams said that Glacier has increasingly been looking at its recycling robots and AI data as two parts of the same flywheel. The data makes the robots better and more accurate, while the robots gather more data with every pick they make.
“What we’re really focused on now is building out that flywheel and also understanding how we can harness that data to solve problems that may even be agnostic of what the robot is immediately meant to treat,” Thrams said. “Our ultimate vision is for Glacier to become a tool that can be an operating system for these recycling facilities.”
The Ecosystem Integrity Fund (EIF) led the round. It also included participation from existing investors including New Enterprise Associates (NEA), AlleyCorp, Overture Climate VC, Amazon Climate Pledge Fund, and VSC Ventures.
New investors in Glacier included Elysium, Overlap Holdings, Cox Exponential, Alumni Ventures, One Small Planet, and Working Capital Fund.
Closing the circular manufacturing loop
To understand Glacier’s long-term goals, you first need to understand how the recycling value chain works. It starts with putting recycling bins out on the curb. Once it’s there, the recyclables are picked up by a truck and taken to an MRF, Hu-Thrams said.
“The job of that MRF is to basically to take that giant pile of commingled recycling, much of which is also trash, and sort it into constituent commodities as effectively as possible,” she explained. “So if the sorting process were perfect, you would end up with these beautiful bales of paper, cardboard, plastics, aluminum cans, and so on that these MRFs could sell to end market manufacturers to turn into new stuff. Now, the sortation process, as you can probably imagine, is extremely cumbersome. It’s very expensive, because much of it is still actually done with manual labor.”
MRFs experience extremely high levels of turnover, and if most MRFs can’t find the workforce, they can’t sort the waste into usable materials. Hu-Thrams said that Glacier is trying to close the loop in circular manufacturing.
Ideally, materials from recycling bins go to a facility, where they are broken down into their individual components, repackaged, and delivered to a manufacturing plant to be made into something else. Right now, however, there’s a broken link in this circle: the MRFs.
“Think about what these MRFs are doing: They’re taking in feedstock, and then their job is to produce a certain yield at a certain quality rate, and do all of the quality inspection you expect out of a typical manufacturing plant,” Hu-Thrams said. “And yet, they have so many fewer tools than something like a plastic bottling plant.”
“They still have a heavy reliance on manual labor,” she added. “They still have little by way of data at scale to help them audit their processes and improve efficiency. That’s really the gap that Glacier is seeking to fill for them.”
Recycling poses sortation challenges
Glacier said its robot costs half as much as conventional options and requires just 3 ft. of conveyor space. | Source: Glacier
MRFs are dealing with an incredibly heterogeneous stream of materials that are dirty and very difficult to sort. This has presented many challenges for companies hoping to automate the process. First, before Glacier, other recycling sortation systems used off-the-shelf robots, which were typically too expensive for the MRF, noted Hu-Thrams.
“Secondly, a lot of these units were just physically large and very space-consuming in an environment that is very space-constrained,” she added. “Imagine a robot that takes up the space of three to four sorters on a sort line and does the job of one.”
Finally, MRFs, like manufacturing plants, live or die based on their upstream,” Hu-Thrams said. “This means they require very reliable systems that can stay running despite the highly variable material stream.
“They’re not just processing bottles and cans and paper, but also seeing things like Christmas lights and surfboards and microwaves and car motors and even things like guns and hand grenades,” she said. “How do you design a system that is versatile enough to work effectively with that kind of material stream? This is why we decided that purpose-built was the way to go.”
Glacier uses off-the-shelf components from reliable OEMs, Hu-Thrams said. The company sourced these parts independently to put together a robot that is compact, has a high uptime, and a faster return on investment (ROI). In fact, Hu-Thrams said a number of Glacier’s customers have gotten their ROI in less than a year. For recycling, a three-year turnaround would be considered fast, she said.
Register now so you don’t miss out!
Glacier helps MRFs get the most from the data it gathers
Throughout our conversation, Hu-Thrams emphasized Glacier’s commitment to putting its customers’ needs first. This is true when it comes to costs, uptime, payment models, customers’ rights to service their robots, and, perhaps most importantly, AI.
“We will go to our recycling facility customers and ask them, what are the commodities, or the types of things, that you care the most about?” Hu-Thrams said. “We’ve actually used that approach to flesh out the way that we’re building our AI taxonomy.”
For example, Glacier works to find ways for its customers to use their data to improve the overall efficiency of the plant. “As we’ve grown out our database and as we’ve grown out the capabilities of AI, we’re actually seeing a large number of customers using the data as a standalone product, like a typical manufacturing plant,” Hu-Thrams said.
“We’ve actually helped numerous customers identify and quantify up to a million dollars in incremental revenue they’re currently sending to the landfill every year, and then we can help them fine-tune their plan and see real-time where those changes made any impact to their overall recovery rate,” she continued.
Looking forward, Hu-Thrams said that she hopes Glacier won’t just be a robotics or an AI data company, but also a partner to help recycling facilities solve top-line issues. For example, if a customer was having problems with contamination in its paper stream, then Glacier could install vision systems and robots in strategic locations to help improve its purity rate.
“We now, perhaps for the first time, can really help these facilities understand in real time, at the item level, what’s going in, what’s coming out in their bales, and what’s being ejected to the landfill,” said Hu-Thrams. “We give them this recovery tool to actually ensure that they’re picking in a particular way.”
GIPHY App Key not set. Please check settings