A single automation success story can spark a transformation. That’s exactly what happened when a leading confectionery manufacturer deployed Robotiq’s palletizing solution in one plant—only to see demand for automation surge across multiple facilities. What started as a local project quickly scaled into a standardized, company-wide rollout, unlocking efficiency, consistency, and cost savings at every level. Here’s how they did it.
The company
For one of the largest confectionery manufacturers in the U.S., growth meant grappling with logistical bottlenecks. With multiple plants producing high volumes of goods daily, palletizing became a pressing concern. The company sought a scalable automation solution that could streamline operations, minimize labor constraints, and enhance efficiency across all locations. The challenge? Ensuring a smooth knowledge transfer between plants and securing buy-in at both local and corporate levels.
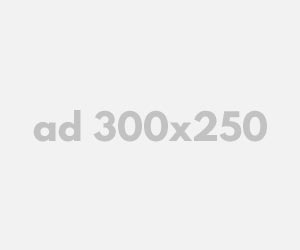
Scaling beyond a single success
The manufacturer initially tested a Robotiq palletizing solution in a single plant. The results spoke for themselves: faster palletizing, reduced physical strain on workersand consistent performance. As word spread through the company’s internal communication network, other plants became interested. However, scaling automation across multiple facilities posed new hurdles:
Knowledge transfer: Individual plants lacked a standardized framework to adopt the solution.
Funding and approval: Each facility had its own capital expenditure (CapEx) budget, creating inconsistencies in deployment.
Alignment with central engineering: Without corporate oversight, widespread adoption could lead to inefficiencies.
Standardization: The secret to scaling Up
Rather than approaching each plant individually, the Robotiq team engaged the manufacturer’s central engineering division. This strategic move provided several advantages:
Standardization: Robotiq’s modular palletizing solution was approved as a company-wide specification, allowing for repeatable and streamlined deployment.
Corporate-level buy-in: Central engineering secured funding for multiple locations, ensuring financial feasibility.
Local and global support: With a network of integration partners, Robotiq balanced standardization with localized support, ensuring minimal downtime and smooth adoption.
Advice for manufacturers looking to scale automation
Start small, scale smart: A successful pilot project can serve as a proof of concept, driving interest across multiple sites.
Leverage internal communication: Share wins internally—videos and testimonials help accelerate buy-in.
Engage central engineering early: Gaining alignment with a central team can unlock funding and ensure a smoother rollout.
Balance standardization with flexibility: A core solution with adaptable components (such as grippers or conveyors) meets varied plant needs.
Partner for local support: A strong network of local integration partners ensures fast response times and continued success.
The bottom line
Automation at scale requires more than just a great product—it demands a structured approach, internal advocacy, and the right partnerships. For this confectionery manufacturer, Robotiq’s palletizing solution transformed from a single-site experiment into a global initiative. With standardization in place and a repeatable framework established, the company is well-positioned to optimize operations for years to come.
Are you considering automated palletizing? Start small, think big, and let Robotiq help you scale.
GIPHY App Key not set. Please check settings