The entire igus campus in Cologne, where it researches, produces, and tests, now covers around 218,000 sq. m (2.3 million sq. ft.). Source: igus GmbH
From motion plastics to humanoid robots, igus GmbH has continued to innovate. Despite economic constraints and geopolitical tensions, the Cologne, Germany-based company yesterday announced that it made €1.105 billion ($1.19 billion U.S.) in sales last year. It is offering a record number of 277 new lubrication-free motion plastics products for 2025.
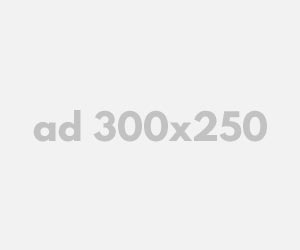
“The changing political and economic conditions didn’t leave us entirely unaffected,” acknowledged Tobias Vogel, CEO for plain bearings and linear technology at igus. “Like many of our customers, we are also focusing on savings and increased efficiency, e.g. through increased automation in our factory.”
“However, our focus is always on the question: What’s in it for the customer?” he added. “These challenges are an even greater incentive for us to break new ground and prove our innovative strength ‘made in Germany’ to reinforce both our competitiveness and that of our customers.”
While the VDMA Robotics + Automation Association has expressed concern that the German robotics industry has lost competitiveness, igus has increased the number of active customers by 5%. The company reported a relatively moderate decline in turnover of 2.5%.
Founded in 1964, igus develops and produces motion plastics, which are lubrication-free, high-performance polymers. The family-run company said it is the global market leader in energy supplies, flexible cables, and plain and linear bearings, as well as lead screw technology made of tribo-polymers. It employs 5,200 people worldwide and has U.S. facilities in Rumford, R.I.
Low Cost Automation addresses more applications
“There is still plenty of potential for innovation in German industry,” said igus, which cited its Low-Cost Automation development work as an example. Its Rbtrx online marketplace includes configuration tools, free consulting and application testing, and numerous products for lean robotics applications.
“We offer over 200,000 parts for automation,” noted Alexander Mühlens, vice president and head of the Low-Cost Automation business unit at igus. “There are too many boring jobs, even inside igus.”
Applications suitable for automation, even at igus, include palletizing and bringing parts to molding and drilling machines, he told The Robot Report during the company’s spring media call.
“We’re starting with AMRs for inside and outside applications,” said Mühlens.
In addition, igus offers help with integrating all the technologies it offers. “Robotics users need to integrate cameras with robots,” he said. “Our answer is the Robot Control software, which makes it easy to integrate cameras with our SCARA robot and ReBeL cobots.”
While about 30% of igus’ collaborative robot arms are used in education, 70% are in industrial applications such as quality control, pick-and-place operations, drilling, CNC machine tending, gluing, and printing, Mühlens said.
At the 2025 Robotics Summit & Expowhich will be on April 30 and May 1 in Boston, igus will demonstrate the following technologies at Booth 221 on the show floor:
The “axis” online community for the industry
The ReBeL EduMove mobile manipulator using open-source software for education and research
The igus Robot Control software
Jan Hennecke, Low-Cost Automation product manager at igus, will present a session on “How to Get Your First Robot Into the Factory” on Wednesday, April 30.
Register now so you don’t miss out!
igus is building its first humanoid
The company is developing its first humanoid robot made of high-performance plastic, particularly for its moving parts. The system is based on igus’ ReBeL Move wheeled mobile robotand ReBeL lightweight cobot arms.
“It can be used flexibly and from any location at different workstations — with a return on investment (ROI) of less than one year,” the company asserted.
As for target markets for its humanoid, igus is open to customer feedback, Mühlens said. Example applications include greeting customers and some insertion and assembly tasks in factories.
“In terms of risk analyses, humanoids are easier to start with in production plants than in restaurants,” said Mühlens, who added that the robot will be designed for safe human-machine interaction.
“Humanoids are the future in a world designed for humans,” he said. “We’ll be presenting at Hannover Messe 2025.”
In line with its motto, ‘Go Zero Lubrication,’ igus is presenting 277 plastic innovations this year, from PTFE-free materials and a complete energy chain series made from recycled materials to a humanoid robot. Source: igus GmbH
Motion plastics leader looks to boost sustainability
In addition to presenting 277 new motion plastics products, igus is continuing to invest in the research, development, and production of innovative technologies. The company said it is producing a version of its igludur plain bearings free of polytetrafluoroethylene (PTFE or Teflon) at similar price points and performance to standard bearings.
igus is converting its entire E2.1 series of energy chains to recycled material from old fishing nets and energy chains that it recycles as part of its It was program. It claimed that this will reduce the CO2 footprint by 80%.
The company said it has reached 92% toward its target of being CO2-neutral with its buildings and production by the end of 2025, measured against Scopes 1 and 2.
“We need to become even better in this area and are working on numerous sustainability measures, from the new multi-story car park with complete façade greening to the modernization of our existing buildings … with photovoltaic systems to the expansion of our MHRS system for heating with waste heat from machines,” explained Michael Blass, CEO of e-chain systems at igus.
The company also announced the igus Mobile Shore Power Outlet (iMSPO) for the shore power supply of container and cruise ships. The system is already in use in ports such as Hamburg, Rotterdam, and Singapore.
With Fraunhofer IPA, igus has developed a new certificate that confirms the cleanroom suitability of its e-chains in long-term tests. They can withstand over 15 million double strokes with minimal and consistent particle emissions, which is important in battery production.
With its emphasis on controlling costs for customers, igus is offering the new G4.42 energy chain for simple gliding applications such as on indoor cranes with travel distances of up to 30 m (98.4 ft.). Thanks to the G4.42’s optimized design, it is not only 12 to 25% lighter, but also 30% to 40% more cost-effective than standard chains of the same dimensions from the E2 and E4 product range, said igus.
The company noted that it has expanded by creating internal startups for systems such as ball bearings, robot drives, 3D printing, and intelligent “smart plastics” for Industry 4.0. It also showed off the mostly plastic RCYL bike, which is currently on a world tour to show the possibilities of recycled materials with igus engineering.
The igus low-maintenance bicycle made from recycled plastic is now on a world tour. Source: igus GmbH
igus invests in German, global presence
“In the last five years, we have invested over €350 million ($377.2 million) in Cologne alone — in land, buildings, state-of-the-art machines, software, new products, people and marketing,” said Vogel.
With last month’s acquisition of elko Verbindungstechnik, which produces cables and plug-in connectors used in machine tools and the automotive industry, igus is building up its assembly capacity in southern Germany. At its Cologne headquarters, igus is investing in automation such as specially developed and patented crimp towers and automated guided vehicles (AGVs) in its factory buildings.
The company has also expanded its production hall and test laboratory in Germany, as well as in its branches in Shanghai, China, and Bangalore, India.
“The customer is at the center of all our activities,” said Blass. “After introducing injection molding in the U.S., we’re now also setting up on-site lead screw production and have opened our own RBTX customer testing area for low-cost robotics.”
“This means that 10 countries now have their own customer test areas so that users can quickly and easily find their individual Low-Cost Automation solution on site,” he said. “Three of these locations — USA, China, Brazil — will be expanded into regional hubs, so that production and development will also be increasingly localized. We are also investing in the expansion of branches in other countries such as Japan, Spain, Taiwan and Poland.”
GIPHY App Key not set. Please check settings