Deere & Co. today announced four new products at CES 2025. The biggest announcement is the addition of full autonomy to the 9 Series tractors, the largest and most powerful tractors in the John Deere portfolio.
The Moline, Ill.-based company also released a fully autonomous sprayer for orchards, announced pilot testing of an autonomous articulating dump truck (ADT) for mining operations, and launched an all-electric, fully autonomous commercial mower that will be released later this year.
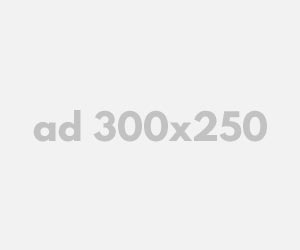
I saw all of the new equipment in action at a November press event at the John Deere farm in Gilroy, Calif. Watching the large autonomous tractors (from a distance) was impressive. Unfortunately, we weren’t able to see the autonomous ADT operate live, due to a sensor failure, but the 5 ft. (1.5 m) diameter wheels of 460E-II ADT demonstrate the scale of self-driving systems.
Deere adds autonomy to flagship 9 Series tractors
The new fully autonomous John Deere 9RX tractor pulls a disc implement. | Credit: The Robot Report
John Deere’s 9 Series tractorswhich have four-wheel drive and up to 830 horsepower, can now be ordered from the factory with an autonomy package, or they can be retrofitted in the field. Available in wheeled (9R) and tracked (9RX) configurations, these powerful machines are the backbone of large-scale farming worldwide, according to Deere.
The company asserted that this move demonstrates its commitment to delivering autonomy across its entire product range. John Deere announced the autonomous 8 Series tractor at CES 2022, and it said it has now completed integration of full autonomy for the top of its tractor line.
The same technology stack that was tested and proven with the 8 Series tractors is now available across both product lines. The system uses components and applications that farmers are already familiar with, including the John Deere StarFire receiver, AutoTrac Turn Automation, and John Deere Operations Center.
Deere added that this opens up possibilities to automate the most difficult agricultural workflows, starting with tilling and cultivation.
When asked about the opportunities for autonomy at John Deere, Chief Technology Officer Jahmy Hindman replied: “If you think of the tillage application, that application is being done generally post-harvest, where you don’t have to see through crop anymore. There’s no standing crop, no mature crop left in the field.”
“But you think of some of these other applications, like self-propelled spraying or harvesting at the end of the year, combine harvesting — there you’ve got a machine that’s interacting with mature crops,” he said. “So this technical difficulty of being able to perceive through a vegetative state that exists with the crop, or seeing through a completely mature state of the crop, and being able to perceive what the environment is like. In those applications, that’s really hard to do.”
Hindman added: “If there’s a sensor modality that we can bring to bear that gives you superhuman capability in the machine, we should do that. So those are some of the technical challenges I think that are still out there. And they’re ones I think that we can solve. It’s just a relatively short amount of time necessary to put in the hard work to figure out the solutions.”
9 Series includes new perception configuration
Front perception cameras on the John Deere 9-series tractors.
The new perception package for the 9 Series tractors moves the sensors up to the roofline of the tractor, providing a complete 360-degree view of the vehicle. The vision processor unit (VPU) is housed to the rear of the cab roof.
The prior generation used obstacle avoidance cameras positioned on the front weight mount of the tractor, explained John Deere.
Tractor offers affordable autonomy for orchard growers
John Deere has fully automated orchard spraying with retrofits for its popular 5 Series tractors. Here is an autonomous 5130ML pulling a spraying tank. | Credit: The Robot Report
For apples, stone fruit, and tree nut growers, spraying is core to their operations throughout the season. Protecting crops like almonds requires repetitive spraying up to 10 hours a day and six to eight times a year.
Traditional GPS systems struggle with accuracy under orchard trees because of the canopy density. Deere’s autonomous diesel tractor, designed for pulling a sprayer in orchards, uses nine cameras, lidars, and sensors to see its surroundings.
Side perception array on the John Deere 5-series tractors.
The John Deere 5130 ML that the company demonstrated during the press event was fully autonomous and attached to an autonomous spraying trailer. It can perceive the entire envelope of the trailer and accurately navigate the orchard rows. The demo followed a “skip row” pattern typical of a manually operated tractor, which allows an easier turn radius through the orchard.
The system still requires an onsite operator to monitor and manage it, but the operator can remain a safe distance away from the spraying, out of the chemical application zone.
Deere autonomous ADT starts trials
John Deere is automating the 460E-II Series of articulating dump trucks, for use in the mining market. | Credit: The Robot Report
Deere’s first autonomous mining equipment tackles the repetitive task of material transport within the challenging terrain of a quarry. This fully autonomous articulated dump truck (ADT) is a behemoth, measuring 34 ft. (10.4 m) long and 12 ft. (3.7 m) high, capable of hauling more than 92,000 lb. (41,730 kg) of material – roughly the weight of seven African elephants – in its bucket.
Constructing a single mile of interstate highway requires nearly 1,900 truckloads, and an average house incorporates around 108 metric tons (120 tons) of sand, gravel, and stone, equivalent to three full truckloads. Deere said this autonomous vehicle will free up valuable human resources, allowing workers to focus on more complex tasks.
John Deere announced that it is beginning trials this year with the autonomous ADT. The quarry environment, where roads are typically well-defined and free of non-construction traffic, provides a good setting for testing and training autonomy technology.
“The great thing about a quarry is it is a structured environment,” said Maya Sripadham, a senior product manager at Deere. “Roads don’t change every day. They might change every couple of months. (It’s the) same with your load and dump locations and the articulated dump trucks — the job is highly repetitive. So it’s a great starting point for construction autonomy and allows Deere to continue to build out our foundational tech stack across all of our equipment to push our expansion forward.”
Current navigation primarily relies on vision, with lidar employed for data collection. Waypoint navigation from pick up to drop off is easily managed via an Operation Center, Deere explained. The company listed key control and monitoring features, including:
Unsupervised operation while allowing customers to track the truck’s activities via the Operation Center
Customer control over the machine despite its autonomous nature
360-degree safety awareness and adherence to predefined paths within user-defined boundaries, all managed through the Operation Center
It said this framework ensures customer oversight while enabling autonomous truck operation without constant direct supervision. Sensors in the bed enable the machine to know how much material is currently loaded, to avoid overloading the truck.
“Of course, our customers always have control over the machine,” noted Sripadam. “It is an unsupervised machine, so it’s capable of running autonomously. You don’t need to watch it at any given time, but you can see what it’s doing, and that’s one of the capabilities that we’re going to turn on through Operation Center.”
Self-driving mowers available for commercial landscaping
John Deere unveiled its first fully autonomous, electric commercial mower. | Credit: The Robot Report
The Robot Report has documented the success of autonomy in the commercial landscaping business. Electric Sheep was honored with the 2024 RBR50 Startup of the Year award for its innovative business model automating commercial landscaping. Now, “Big Green” has plans to dominate this market with the upcoming launch of its first electric and fully autonomous commercial mower.
The new mower boasts a 21.4kWh battery, enabling up to 10 hours of continuous operation while being quieter and easier to maintain than a gas-powered mower, according to Deere.
The perception stack uses only cameras to see the world around the mower, which includes John Deere’s existing “Generation 2 autonomy stack” that it developed for larger machines like tractors and sprayers.
Deere’s autonomous mowing system is equipped with the Starfire GPS receiver, honed over two decades of development, to ensure precise location data. At its core lies a rugged vision processing unit (VPU), a common component across the company’s autonomous offerings. It noted that this autonomy package is designed for seamless factory integration into the mower, eliminating the need for retrofitting.
John Deere has not announced a release date for the new autonomous mower yet but is planning to release it in the second half of 2025.
Register today to save 40% on conference passes!
GIPHY App Key not set. Please check settings