The RDS fleet management system can serve in scenarios such as multilevel movement. Source: SEER Robotics
Under the wave of Industry 4.0, robotics technology is increasingly permeating production and logistics processes. However, achieving efficient collaboration and optimal resource allocation in complex multi-machine operations, cross-regional scheduling, and diversified scenarios remains a critical challenge. SEER Robotics said its M4 Smart Logistics Management System, powered by its core module—the RDS Fleet Management System—offers an innovative solution.
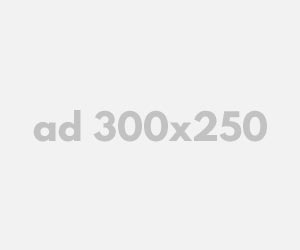
The Shanghai, China-based company explained how its Resource Dispatch System (RDS) fleet manager can elevate efficiency across four diverse scenarios through intelligent scheduling.
RDS enables cross-floor, cross-region collaboration
In large factories, tasks spanning multiple floors and regions are becoming commonplace, requiring robots to coordinate with elevators, automated doors, and other smart devices. SEER Robotics said its RDS system acts as a “central neural network” by integrating with enterprise-level business software such as manufacturing execution systems (MES) to enable data exchange and task distribution.
Case study: Zhejiang Tailin Bioengineering
Zhejiang Tailin Bioengineering’s RDS system interfaces with its MES, enabling automatic task allocation and robot execution. For instance, during cross-floor transportation, the system dynamically synchronizes elevator schedules with robot routes, ensuring smooth task transitions.
The company can also initiate tasks via MES and monitor logistics in real time, achieving increase in cross-floor operational efficiency.
Dynamic global planning resolves congestion
In complex environments with narrow aisles or human-robot collaboration, path conflicts and congestion are frequent. The RDS system employs dynamic global planning to analyze real-time robot positions, task priorities, and environmental changes, optimizing multi-robot pathfinding and traffic control to prevent deadlocks.
Case study: WINFAT Holdings
With 44 intelligent forklifts under RDS coordination, the system resolved path conflicts during peak operations at WINFAT Holdings Ltd. By dynamically adjusting routes and prioritizing tasks, the company achieved 100% accuracy in human-robot collaboration and a 300% boost in overall production efficiency.
Pre-Loading Mode eliminates empty runs
Empty robot runs are a common source of resource waste in logistics. The RDS system introduces innovative “ride-sharing” and “pre-loading” modes. Using global task-allocation algorithms, it assigns new tasks to robots nearing completion and directs multi-warehouse robots to pick up goods from the nearest locations, minimizing idle travel and enhancing warehouse efficiency.
Case study: Chinawrr Automated Pallet Warehouse
Using real-time RDS data, Chinawrr’s warehouse dynamically adjusts inbound/outbound task allocation, achieving a unilateral throughput of 290 pallets per hour and a 20% increase in storage efficiency, with empty runs reduced to below 5%.
Production beats simulation: Precision deployment of robots
In precision manufacturing, controlling production beats directly impacts efficiency and quality, said SEER Robotics. The RDS system enables rapid simulation modeling, allowing companies to test robot deployment by dynamically scaling robot numbers and simulating concurrent tasks.
Case study: Electrolux’s Swedish factory
SEER Robotics’ RDS system optimized robot-system interfacing and resolved communication delays in semi-finished product transportation. This reduces production beat errors to a much lower level and increases output capacity for Electrolux.
RDS and the future of fleet management
The RDS system’s value lies in its “global optimization” logic and “dynamic adaptation” capabilities, according to SEER Robotics. By driving decisions through data, it can enhance cross-regional collaboration, complex path planning, and resource utilization.
As artificial intelligence and Internet of Things (IoT) technologies converge, the fleet management system will further transcend scenario limitations, becoming the core engine of industrial automation, the company said.
Register now so you don’t miss out!
GIPHY App Key not set. Please check settings